Inspection & Maintenance
We provide Inspection, Testing & Maintenance Services for Fall Protection & Access Systems
This equipment is safety critical.
We understand that inspection of safety critical equipment is not an exercise of slapping inspection tags onto them. We take all of our inspections seriously and take guidance from all the current relevant British Standards & Manufacturers Guidance to ensure your equipment is not putting you at risk. See below for our approach & Inspection process.
Anchor Systems
Regulation 16 within the working at height regulations confirms that the duty holder (e.g. building maintenance manager, building owner) has a responsibility to ensure that work equipment for working at height is appropriately inspected. We work to the latest standard BS 7883:2019 for all our inspections of anchor systems. This latest revision of the 2005 standard contains a clearer outline for what is expected for a Fall protection anchor system (both currently and retrospectively) and has a detailed category of results (Fail, Conditional Fail, Conditional Pass and Pass) depending what conditions the anchor system has met, from design records, system calculations, O&M information to the system technical file. HeightLink have the process in place to carry out a full BS 7883:2019 compliant Inspection and provide the relevant documentation to comply with this onerous British Standard. We also can provide the correct testing & documentation for any anchor systems intended for Rope Access that need to comply with The Lifting Operations and Lifting Equipment Regulations 1998 (LOLER)
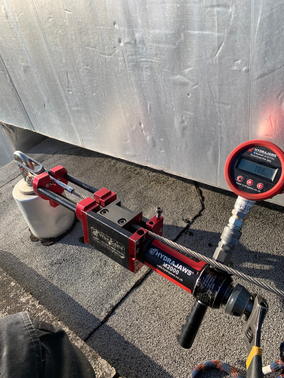
Under BS 7883:2019 all anchor systems installed prior to this standard require an installation review on inspection
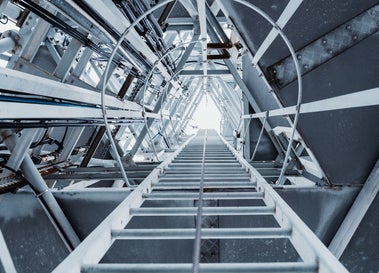
Access Equipment
Equipment such as Ladders, Guardrails and Walkways in the work place are covered under The Provision and Use of Work Equipment Regulations (P.U.W.E.R) 1998, where the “Duty Holder” must ensure that any work equipment provided is suitable for use, maintained and inspected.
It is the duty holder’s responsibility to ensure that prior to use, equipment provided is inspected by a competent person. It is recommended that this equipment is inspected at frequencies not exceeding 12 months.
Personal Fall Protective Equipment
HSE INDG367 recommends a detailed examination is carried out on Personal Fall Protective Equipment at least 6 monthly. This may be increased depending on the frequency of use and conditions in which the equipment is being used in. All inspections carried out by HeightLink Fall Protection Services follow guidance from INDG367, BS 8437:2005 & BS 365:2004.
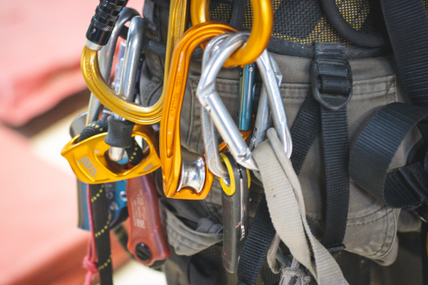
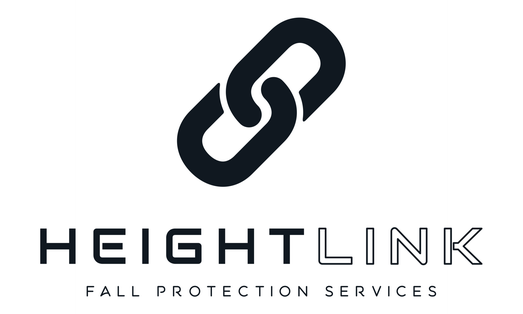
Why Choose HeightLink Fall Protection Services?
-
We will ensure your equipment is inspected within the latest British Standards & manufacturers guidance that they should be to ensure our clients meet their statutory demands
-
Full Inspection Reports, O&M and System Technical Files issued
-
Our services cover the entire UK
-
Commitment to delivering the best quality work for our clients